Making our signs
Our green signs are a well-known sight across Scotland and welcome thousands of people to our forests every year. But have you ever wondered how they’re made? In this article, we take a trip to Border Signs and Graphics in Dumfries to find out.
With over 300 forests across Scotland, numerous offices and hundreds of miles of off-road trails, we need a lot of signs. Recently that has been the job of Borders Signs and Graphics in Dumfries. We’re here to meet David who is going to show us how they turn a rough wooden board into one of our distinctive green signs.
To start with, the vast majority of our signs are wood. To be precise, Douglas fir sourced from several forests in Scotland. This is a good and strong wood, soft enough to carve but tough enough to stand the test of time, and crucially it can take paint well (unlike some other species). Wooden boards around 6 feet long arrive in the workshop on a large pallet. It looks a lot, but David tells us they can turn all of it into signs and boards in just a couple of days.
The rough boards first need to be made clean, straight and flat. That means running them through the planer. The rotating blades on this machine make a perfectly flat surface on one face of the board, before the operator does the same on one edge, running the board along a fence. This makes for a perfect 90° edge on one side. The same machine is then adjusted to become thicknesser which can make the remaining rough face and edge perfectly flat and parallel to the first face and edge. It also takes every board down to the same uniform thickness.
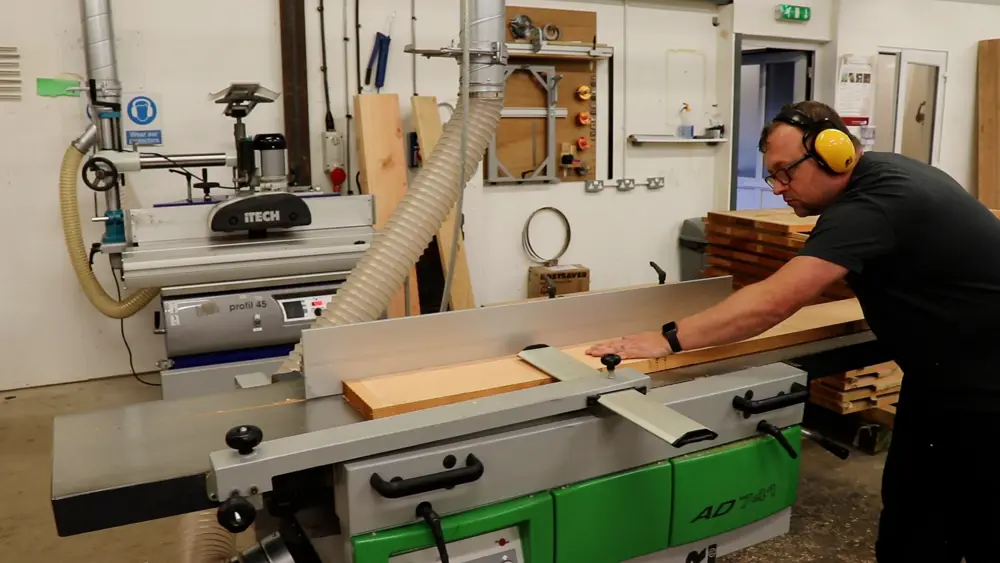
Every board in the workshop goes through this machine to get cleaned up with flat and square faces and edges.
For some large signs, several boards need to be glued together. With the edges already planed flat, they can be glued straight away. After applying the glue, the boards go on a special table and are clamped together with pneumatic clamps.
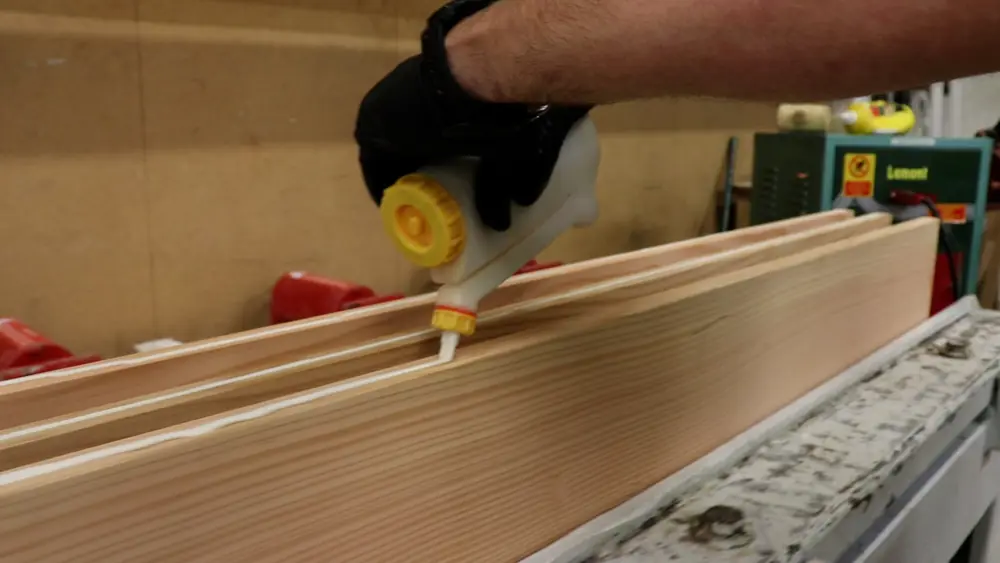
Applying glue to the edges of several boards
Every workshop wants to be efficient, so waiting a day or more for glue to fully dry and cure isn’t ideal. That’s where the Wood Welder comes in. This machine is pressed on select areas of the glue join and using radio waves (similar to how a microwave works), cures that area of glue in seconds. After this has been applied, the complete board can then be used straightaway. The dried glue holds the board together firmly while the rest can set in its own time, allowing the team to get working on the next process.
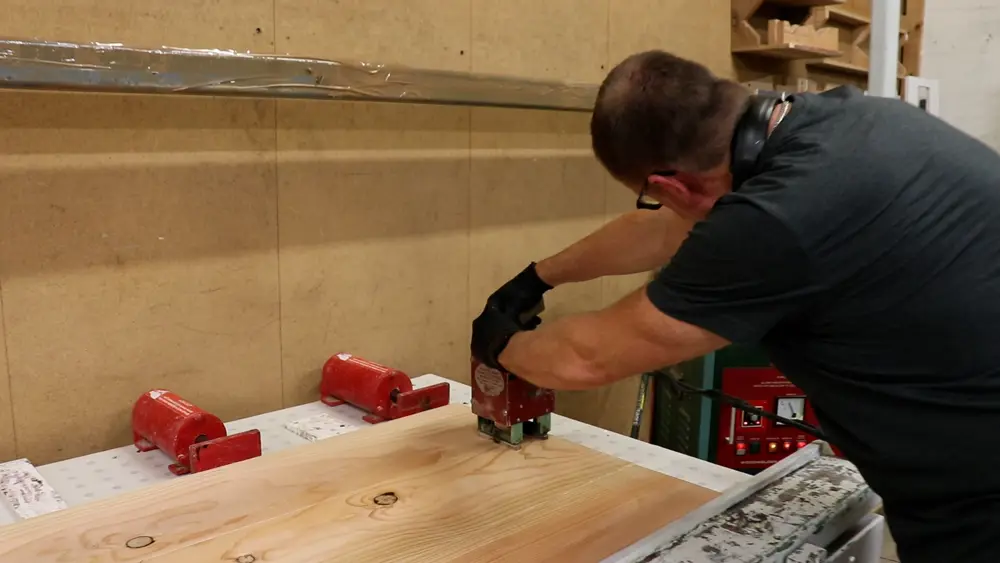
The Wood Welder in action. This allows the board to be used straight away, rather than waiting for the glue to dry.
CNC
The next stage is where the real magic happens. A CNC router can carve virtually any shape into the wooden boards. From place names to symbols, if it can be created on a computer, it can be carved into the wood. David chooses a file to load and puts a board into the bed of the machine. At about the size of a snooker table, they can carve into large boards or many small ones simultaneously. Once strapped down, we hit ‘play’ and the machine goes to work.
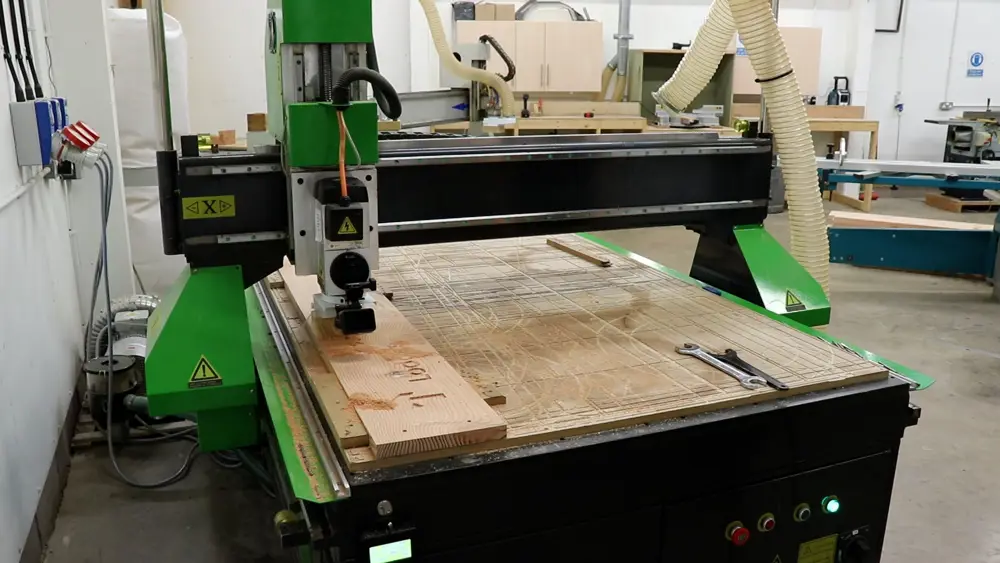
The CNC router in action
The spinning router cutter takes many light passes to create the depth required for each letter and symbol. It moves back and forth, up and down, never erring. Similar to how your home printer works, but far more impressive and capable. It carves our sign in about 10 minutes, though David says he’s slowed it down for us to film – it’s normally a fair bit quicker. There’s an impressive amount of chips made, but again that’s not normally the case – the extractor has been removed so we can better see the router in action.
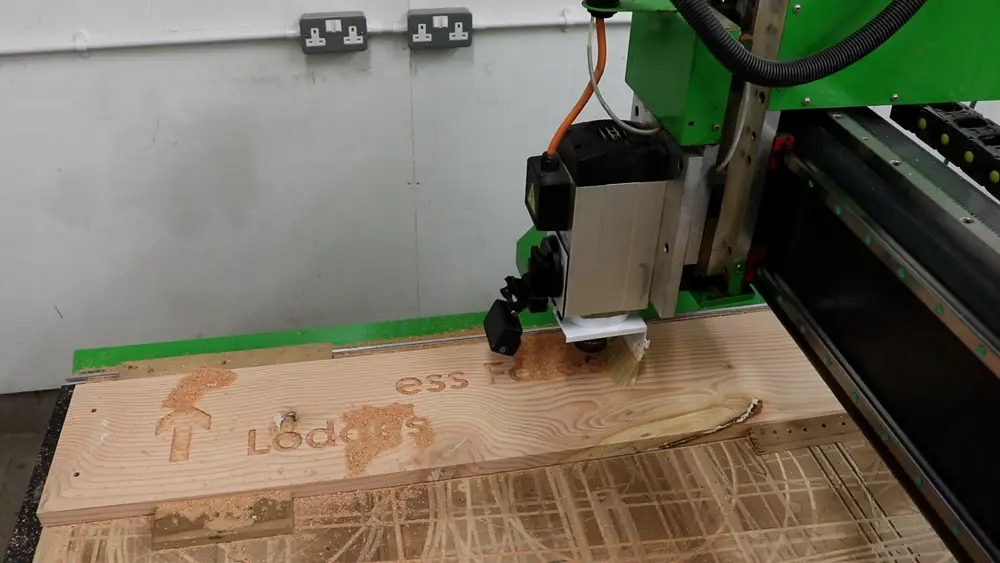
Our sign being carved
The board is now a bare sign, and looks great. Our signature rounded font comes out of the machine perfectly, but there are still some things to do before we can get painting, namely sanding.
First up is a trip through the drum sander. This removes any little burrs and frayed edges from the router. Then the edges are sanded smooth with a very large belt sander. Finally, the board gets a couple of minutes with a random-orbit sander to leave a smooth finish for painting.
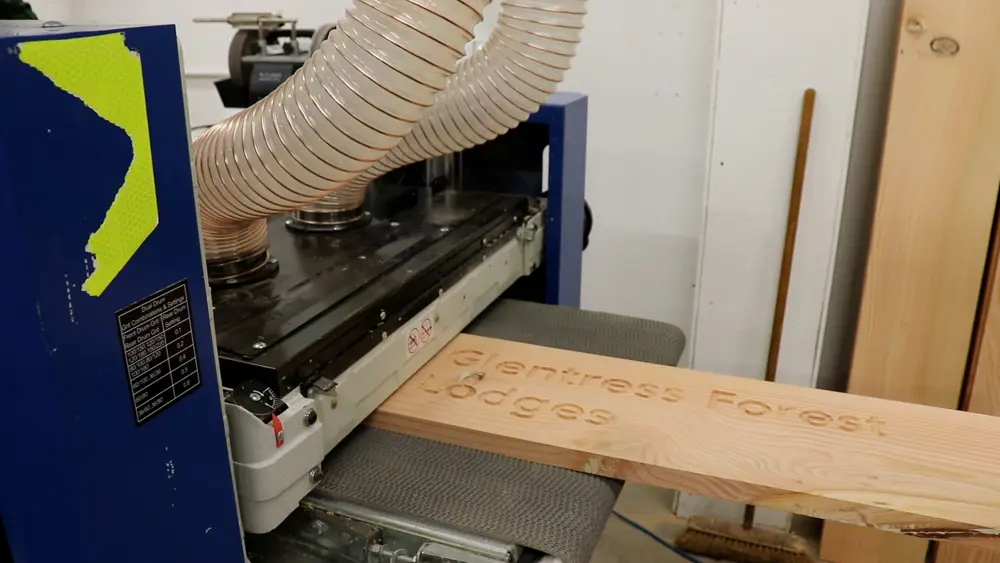
The drum sander removes any burrs or tears the CNC machine may have left on the surface.
Paint
The paint shop is separate from the main workshop. Whilst every machine in the workshop is hooked up to a dust extraction unit, there’s still dust and wood chips around which don’t mix well with paint. Next door, the paint shop is noticeably quieter (no ear plugs required here), with good ventilation.
The signs are checked for knots, and where there are any, each knot is sealed to ensure the paint will stick on that area. A paint sprayer is used to apply a coat of primer, and later on, it’ll put on the required coats of our signature green paint. Finally, it’s time for the details.
The carvings typically require white lettering, so the board is carefully masked up with plenty of masking tape and careful use of a scalpel. Once ready, the lettering can be painted on, typically by hand. With some signs requiring multiple colours (like additional red and black for a speed limit), it can take a little while to allow each colour to dry before moving on.
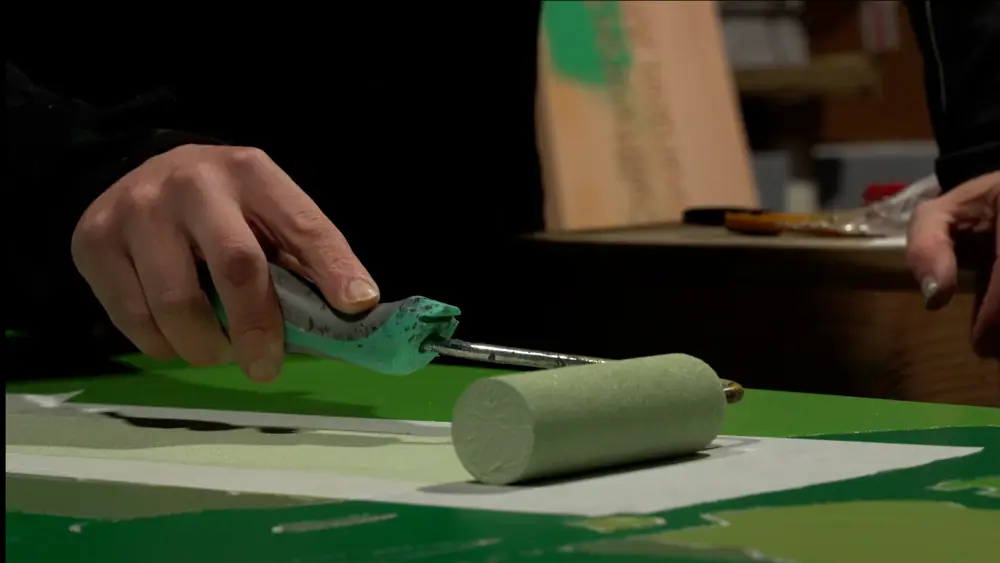
Using a paint roller on a masked section of sign
We’re lucky to see a large welcoming sign be completed with a last little coat. This one has several shades of green and is bigger than your average front door. When the masking tape is peeled off, the whole sign pops under the lights. Once dry, it’ll be wrapped up ready for delivery. Along with the hundreds of others ready and waiting!
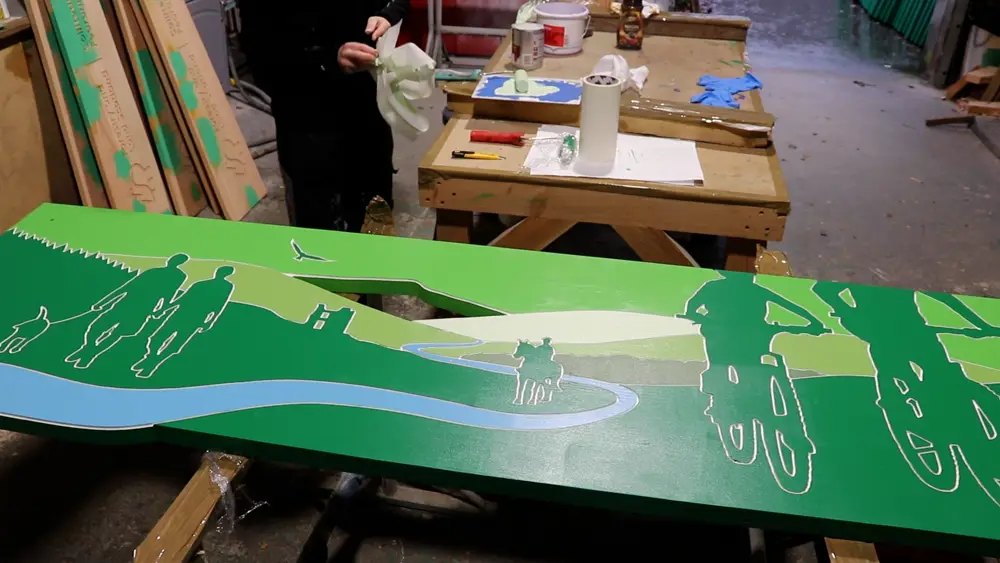
A finished sign ready for installation.
As a final bonus, we have a quick look in the print shop. This really is like your home printer but enlarged to the size of a family car.
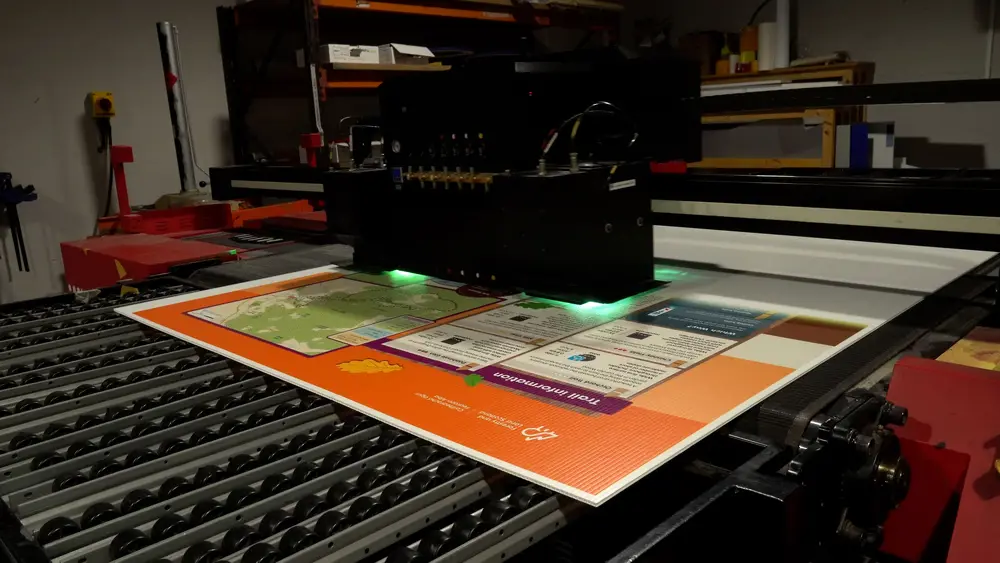
The large printer can make truly massive signs and information boards
With care, each sign can last many years, though it does depend on where they are sited. Ultimately though, even old wooden signs can be sanded down and re-painted, or re-purposed for something else, making it a fairly sustainable process. It’s really great to see one of the most distinctive and visible parts of our forests taking shape.
Many thanks to David and the team at BSG for hosting us!